 Книжкові видання та компакт-диски  Журнали та продовжувані видання  Автореферати дисертацій  Реферативна база даних  Наукова періодика України  Тематичний навігатор  Авторитетний файл імен осіб
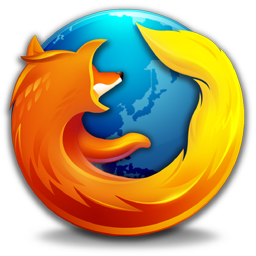 |
Для швидкої роботи та реалізації всіх функціональних можливостей пошукової системи використовуйте браузер "Mozilla Firefox" |
|
|
Повнотекстовий пошук
Пошуковий запит: (<.>A=Sakhno Y$<.>) |
Загальна кількість знайдених документів : 4
Представлено документи з 1 до 4
|
1. |
Konova E. M. Mechanical and Optical Properties of Polytetrafluoroethylene Treated by γ-Irradiation Near the Melting Point [Електронний ресурс] / E. M. Konova, Yu. E. Sakhno, S. A. Khatipov, V. G. Klimenko, S. T. Sychkova, T. V. Sakhno // Фізика і хімія твердого тіла. - 2011. - Т. 12, № 4. - С. 1013-1017. - Режим доступу: http://nbuv.gov.ua/UJRN/PhKhTT_2011_12_4_32 Radiation-modified polytetrafluoroethylene (PTFE), which exhibits intense fluorescence in the visible spectral region, was prepared. Radiation modification was performed with <^>60Co rays at 330 C, at a dose of 0,2 MGy. The mechanical properties, fluorescence and electronic absorption spectra of film and block PTFE specimens irradiated under the given conditions were studied.
| 2. |
Kalchenko V. V. Determination of the cutting force components while milling cylindrical surfaces with an oriented tool [Електронний ресурс] / V. V. Kalchenko, S. D. Tsybulya, A. V. Kolohoida, Ye. Yu. Sakhno, S. V. Boyko // Науковий вісник Національного гірничого університету. - 2021. - № 2. - С. 82-88. - Режим доступу: http://nbuv.gov.ua/UJRN/Nvngu_2021_2_14 Purpose. Construction of a general modular mathematical spatial model of the removal allowance process and shaping when milling round surfaces of rotation, such as camshaft necks, cylindrical surfaces of gearbox shafts and others. Determination of the components of the cutting forces when machining with crossed axes of the milling cutter and part in order to use the results when assigning machining modes. Methodology. Theoretical development of a modular mathematical model of the removal allowance process and shaping during milling of cylindrical surfaces was carried out using a matrix apparatus for converting coordinate systems. Unified modules were developed: instrumental, orientation and shaping, which allowed us to describe the processing of the part more clearly. All calculations were performed in the mathematical package Mathcad. Using the functions available in the package, a graphical representation of the mathematical model of the tool and machined surfaces was obtained. Using the logical blocks developed in the program, the characteristics of the treated surface were investigated, such as roughness in the axial and radial planes. The influence of the tool orientation angle and the number of cutter teeth on the roughness of the machined surface was investigated. The known formulas for calculating the cutting forces during milling are specified. Findings. A general modular mathematical spatial model is constructed of the removal process of an allowance and formation at milling by the oriented tool of round surfaces of rotation, such as necks of camshafts, cylindrical surfaces of shafts of transmissions and others. The roughness parameters of the treated surface are determined. The outflow of the tool characteristics and the angle of its orientation on the geometric roughness in the axial and radial sections is investigated. The area of the layer cut off by one tooth of a mill is defined. The calculation formulas are specified for finding the components of cutting forces during milling. Originality. A modular spatial model of the process of milling cylindrical surfaces with an oriented tool is proposed, on the basis of which the components of cutting forces are calculated, which can be used in designing new tools and improving machining conditions by the existing ones. Practical value. Based on the use of modern computer facilities and software, the developed calculation program allows controlling the process of forming cylindrical surfaces during their milling with an oriented tool. It also allows predicting the initial machining accuracy by determining the parameters of geometric roughness in axial and radial sections. This makes it possible to choose the optimal tool orientation angle, milling cutter parameters and cutting modes to achieve high productivity and processing quality.
| 3. |
Sakhno Y. I. Condition-based switching the multicomponent reactions of 5-amino-3-(methylthio)-1,2,4-triazole, aromatic aldehydes, and pyruvic acid [Електронний ресурс] / Y. I. Sakhno, M. V. Mykhailenko, M. A. Kolosov, E. H. Shvets, V. I. Musatov, N. V. Chorna, S. M. Desenko, V. A. Chebanov // Ukrainica bioorganica acta. - 2020. - Vol. 15, № 2. - С. 22-26. - Режим доступу: http://nbuv.gov.ua/UJRN/Uba_2020_15_2_5
| 4. |
Kalchenko V. V. Simulation of the process of milling and grinding cylindrical surfaces by an oriented tool in one setup [Електронний ресурс] / V. V. Kalchenko, V. I. Kalchenko, S. D. Tsybulya, A. V. Kolohoida, Ye. Yu. Sakhno // Naukovyi visnyk Natsionalnoho Hirnychoho Universytetu. - 2022. - № 4. - С. 66-70. - Режим доступу: http://nbuv.gov.ua/UJRN/Nvngu_2022_4_13 Purpose. Improvement of schemes for processing the cylindrical surfaces of the shafts of gearboxes and transmissions of large-sized equipment. Development of modular spatial models of the processes of milling and grinding of the cylindrical surfaces of the shafts of gearboxes and transmissions of military and civil vehicles. Development of a model for dressing a grinding wheel with a diamond tool. Methodology. Creation of general and particular modular mathematical models of the processes of removal of allowance and shaping during rough and finish milling and finishing grinding of non-rigid cylindrical surfaces was carried out using a matrix apparatus for transforming coordinate systems. This made it possible to describe the treatment process using standard matrices. The calculations were carried out in the mathematical package Mathcad. To obtain a graphic display of the mathematical model of the instrumental and machined surfaces, the standard functions of the software package and the developed logical blocks were used. Findings. A technique for processing cylindrical surfaces of revolution with an oriented tool is proposed. Roughing, finishing and polishing are carried out in one setup. Roughing and finishing are carried out with an oriented cutter with replaceable multifaceted carbide inserts. The angle of orientation of the cutter is selected from the condition of maximum loading of the end section. Thus, the roughing stock is removed by the end face and by the finishing periphery, while the maximum component of the cutting force is directed along the axis of the part and does not cause deformations in the radial direction. Final finishing is carried out with a wide grinding wheel. The angle of orientation of the grinding wheel is selected from the condition of uniform distribution of the allowance along the periphery. A scheme for dressing the working surface of a grinding wheel with a diamond pencil with a constant feed is proposed. Originality. Modular spatial models of the processes of milling and grinding of the cylindrical surfaces of the shafts of gearboxes and transmissions of military and civil vehicles were developed. A model for dressing a grinding wheel is proposed. The use of the proposed models makes it possible to conduct a more detailed analysis of the processes of stock removal and shaping. Practical value. Dependencies are proposed for choosing the optimal angles of orientation of the cutter for roughing and finishing milling and the grinding wheel for finishing. The accuracy of parts is increased due to the elimination of the resetting error. The cost of manufacturing is reduced due to the maximum full use of cutting carbide inserts, by turning them and operating the worn finishing edge in the rough milling mode, as well as by increasing the resource of the grinding wheel.
|
|
|